Quality Manager
Location | Kampala, Uganda |
Date Posted | July 26, 2024 |
Category |
Management
Quality Assurance |
Job Type |
Full-time
|
Currency | UGX |
Description
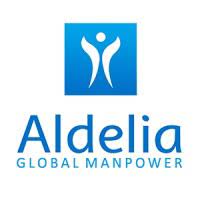
About the Company:
Aldelia is a global leading human resources company founded in 2005 and specialised in recruitment, outsourcing and payroll management services to blue-chip multinationals and fast-growing SMEs. The group operates in more than 30 countries across all industries and disciplines on four continents. Our mission is to create a better future for people by delivering compliant, world-class and innovative HR solutions to the companies and communities we serve.
Job Summary: The Quality Manager will ensure that products manufactured and supplied by our client are fit for purpose, are consistent in quality, supply, and meets both internal and external requirements and it includes legal compliance and customer expectations. Drive systems (QMS, OH&SMS) and Ensure the implementation and continual improvement for all processes.
Key Duties and Responsibilities:
- Oversee Quality Assurance and Control practices for the our client.
- Oversee inspection of all incoming raw and packaging materials and ensure compliance with our client internal quality standards.
- Ensure full compliance of all products with all government safety regulations.
- Interact effectively with UNBS and other regulatory bodies, system safety auditors and customers to maintain positive and responsive relationships and assure rapid corrective actions through dynamic leadership and timely documentation.
- Develop, schedule, and direct Quality and Occupational Health & Safety
- Management Systems audits and monitor corrective actions to non-conformities for completion and effectiveness, providing gap closure assistance to factory activities.
- Validate and assure compliance with established environmental safety and quality objectives through daily monitoring programs, team supervision, and ensure that there is control of unintended use of non-conforming product or material produced in-house, or in the company stock.
- Responsible and accountable for disposition of non–conforming product based on quality checks/ and inspection results.
- Establish new and improved quality & safety programs, policies and procedures to ensure that established standards of quality are consistently measured, documented and maintained.
- Provide product safety risk assessment information, new information and risk management strategies.
- Proactively identify potential and emerging product safety issues and develop strategies to effectively investigate and address arising concerns.
- Conduct quality training programs to all employees with emphasis on product quality, customer feedback and continuous improvement through identification and analysis of customer requirements.
- Conduct root causes and corrective actions from product quality defects/ consumer/ customer complaints and implement corrective actions with plant operations team.
- Responsible for implementation and enforcement of environmental legal requirements in the plant.
- Participate in operations review meetings with other sectional team leaders and oversee implementation of actions related to quality and environment.
- Maintain a comprehensive database of all products manufactured as well as raw materials, packaging materials, and operations in the manufacturing process including in-process quality specifications and standards.
- Provide a source for data related to quality of raw and packaging materials, products, customer feedback and give an analysis that guides decision making.
- Deliver on the implementation of our clients Way / Industrial Best practices.
- Other duties as may be assigned by your supervisor.
Qualifications, Skills and Experience:
Academic:
- A University degree in Industrial Chemistry, Chemical Engineering, Chemical and Process Engineering, or any related field.
Professional:
- Trained in Analytical techniques/ Injection molding production technology
- Trained ISO Systems Auditor/ NEMA Lead or Associate Auditor
- Trained in Six Sigma; yellow/green/ black or master black belt
Experience:
- Minimum of 3 years experience in the plastic molding sector in a manufacturing firm.
- Experience in product development and process improvement projects.
- Experience working with third parties/ suppliers/government departments.
- Solid understanding of environment, safety, health and quality management systems; HACCP, ISO, cGMP, TQM
- Analytical approach and problem diagnostic skills.
- Solid understanding on implementation of industrial best practices.
- Strong leadership and communication skills
- Computer literate – preferably statistical packages.
Specialist knowledge required:
- Working knowledge of Occupational health & safety, and Quality Management Systems; HACCP, ISO, cGMP, TQM
- Knowledge in product development preferably in plastic manufacturing.
- Use of modern process improvement tools and techniques – Statistical Process Control and Six Sigma
- Excellent in data analysis, report preparation and presentation
- Proficiency in computer applications in MS Office and statistical packages.
Behavioral Competencies:
- Proven ability to maximize output from teams.
- Strong ability to think through and analyze complex quality problems
- Strong commercial mentality and creativity.
- Confident, enthusiastic and passionate person
- Ability to manage and deliver on complex projects.