Quality Assurance Manager
Location | Kampala, Uganda |
Date Posted | May 26, 2025 |
Category | Management Quality Assurance |
Job Type | Full-time |
Currency | UGX |
Description
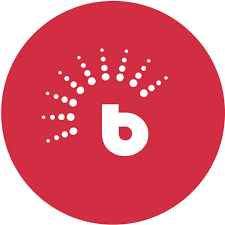
Job Summary
To build robust Quality Management Systems compatible with best practices. The systems should not only address proper quality aspects but also ensure sound scientific and technical performance in line with current Good Manufacturing Practices (cGMPs).
- Minimum Qualification : Bachelors
- Experience Level : Mid level
- Experience Length : 5 years
Job Description/Requirements
Department: Quality
Reporting to: Head of Quality
Staff Level: ExCo -1
Location: APDL-Mukono
POSITION PURPOSE:
To build robust Quality Management Systems compatible with best practices. The systems should not only address proper quality aspects but also ensure sound scientific and technical performance in line with current Good Manufacturing Practices (cGMPs).
JOB ROLES AND EXPECTATIONS:
Quality Management
- Develop, implement, and maintain up-to-date Integrated Management systems (QMS, OSHMS, EMS), processes and procedures in line with current Good Manufacturing Practices (cGMPs).
- Conduct Quality Systems Management Review (QSMR) and report trends of Quality systems i.e., Change Controls, Deviations, Market Complaints/Recalls, Out-of- Specification (OOS) results, product recalls, Training, CAPAs, Annual product reviews, among others.
- Prepare, Review and maintain Contamination control strategy, IMS/Quality Manual, Site Master File, Validation Master Plan and Quality plan.
- Participate in Risk management activities including Identification, assessment, control, review and reporting.
- Establish and maintain a qualification, validation and maintenance program for equipment, systems, and processes.
- Establish a system of internal audit to assess compliance with IMS and cGMP requirements, company policies and procedures.
- Perform Vendor audits and qualification of new and existing suppliers of critical starting materials, consumables, components, and services and maintain Quality agreements with approved suppliers and contractors.
- Investigate and report market complaints/Recalls and provide feedback to customers timely.
- Establish and implement appropriate in-process controls during manufacturing operations to ensure consistent delivery of quality products.
- Ensure laboratory testing and release of components, containers, in-process materials, packaging materials, and drug products is done according to approved specifications and methods.
- Review and approve all Quality Assurance documents, such as BMRs, procedures, protocols, test methods, and specifications.
- Conduct investigations to determine the root cause of product/system/equipment/process failures, Non- conformities, audit gaps, deviations, out of trends, and approve Corrective actions to ensure continuous improvement.
- Establish a training program for all personnel involved in manufacturing and ensure qualification of personnel as per their job requirements.
- Review and approve Completed Batch manufacturing and quality control records and ensure batch release as per marketing authorization.
Customer Service
- Deliver all activities within service level agreements (SLAs) to ensure timely delivery to customers.
Records Management
- Responsible for Issuance, Archiving, Retention and Destruction of all controlled documents and records.
Operational Cost Control
- Participate in the Budgeting process and execute QA activities within the allocated resources.
Leadership
- Lead, mentor, and coach the teams under your Supervision to ensure that they are motivated.
- Manage team performance, training, and succession planning initiatives
Technical Skills and attributes:
- Strategic mindset with hands-on execution
- Strong analytical and problem-solving skills
- Excellent written and verbal communication
- Ability to manage cross-functional teams
- High integrity and attention to detail
- Budget Management
- Negotiation skills
- Competence in understanding the chemist and analysis
- Auditing skills
Behavioral Competencies:
- Collaboration and Team work
- Time Management
- Agility
- Integrity
MINIMUM QUALIFICATIONS / REQUIREMENTS:
- Bachelor’s degree in pharmacy.
- Relevant Postgraduate qualification is an added advantage.
- Minimum of Ten (10) years of progressive experience in pharmaceutical manufacturing industry
- Minimum of Five (5) years’ experience at a Senior Management level
TRAINING REQUIREMENTS:
- Basic safety training
- Basic GMP training
- Leadership training